Drying

In the dewatering unit, the gas bubbled up through a number of trays of triethylene glycol. This chemical absorbs water, so that the gas emerging from the top of the dewatering unit was dry. Water-free glycol was pumped into the top of the tank, and the “wet” chemical drawn off close to the bottom.
From the dewatering unit, the gas passed to metering stations and control valves before being exported to Scotland through one of two 32-inch pipelines.
Glycol regenerator
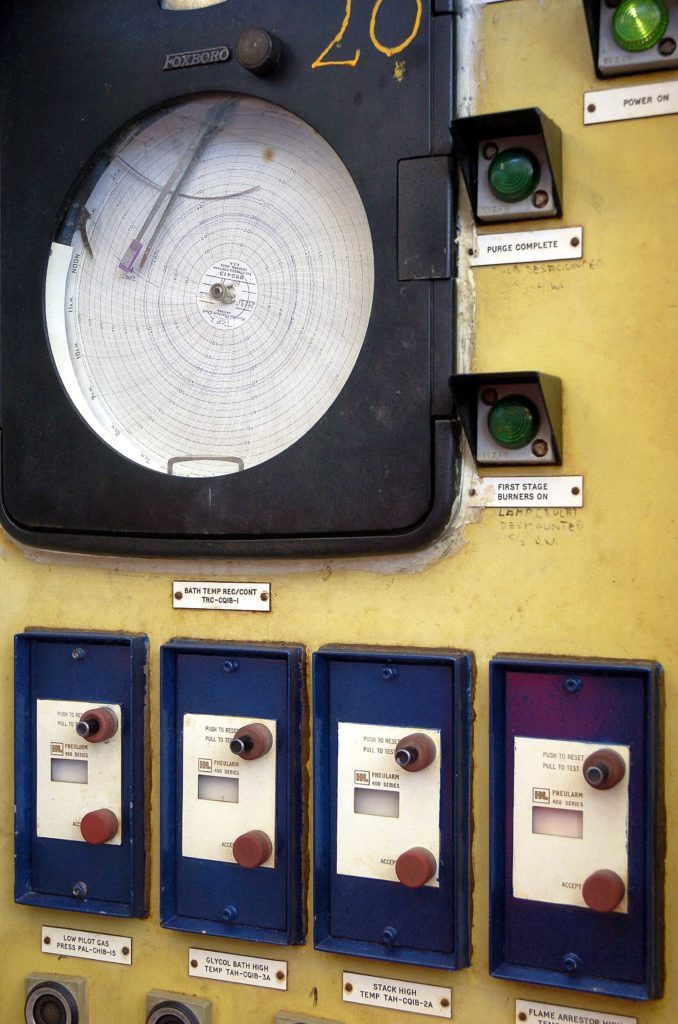
The glycol removed from the gas dewatering unit had absorbed water, which needed to be stripped out before the chemical could be re-used. This was done in the regenerator unit, where the glycol was heated until the water evaporated.
Wet glycol was sent first to a separator where possible hydrocarbons were removed. The next step went to a heat exchanger and glycol heater, where the chemical was heated to a maximum of 204°C so that the water evaporated. After being cooled in the heat exchanger, the glycol was piped to a collection tank and pumped back to the gas dewatering unit.
The temperature in the heater unit was crucial for the dryness of the glycol, which in turn determined how dry the gas would become. Adjusting the heater temperature accordingly made it possible to control gas dryness.
Operator
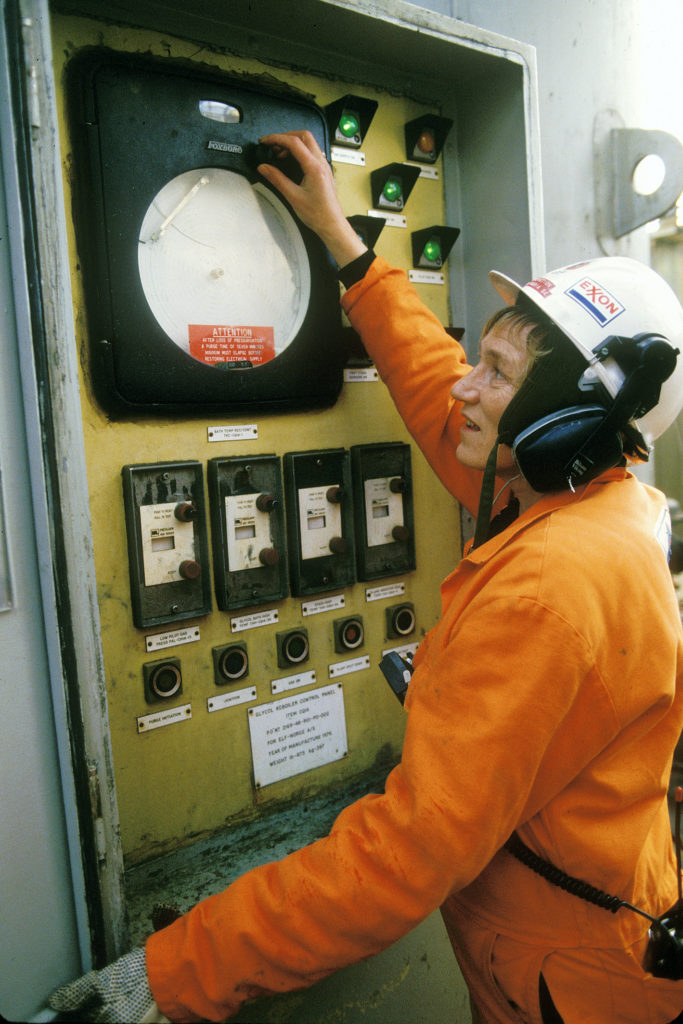
After condensate and most of water had been separated out, the gas went to the glycol contactor for any residual water to be removed.
The gas entered the bottom of the column and bubbled up through the glycol, which was added from the top. A carbohydrate-based product, glycol is comparable with the anti-freeze used in car radiators and has a great affinity for water. The gas ascended through a series of trays containing glycol, thereby maximising contact. When the gas emerged from the top of the column, it was completely dewatered and could be piped to St Fergus. The glycol emerging from the base of the column was heated and dewatered in a regenerator for re-use.
The operators, together with a laboratory assistant, checked this process several times a day. Samples were taken to check glycol quality. An abnormally low water content meant the chemical was unable to absorb enough of it, and might have to be replaced. The job of the operators was to ensure that the gas was dry enough to be piped to the UK. That was determined by the “dryness” of the glycol and how much water it could absorb. This parameter was adjusted through the temperature of glycol regeneration.

Three operators in each shift on the process platforms worked as a team. One was responsible for the compressors, one for the rest of the process, and one for gas dewatering. The last of these was a busy job, with many small adjustments, and called for a dedicated operator in charge of the whole glycol system. This person monitored the process out in the modules through physical inspection of the equipment.