The Frigg Transportation System
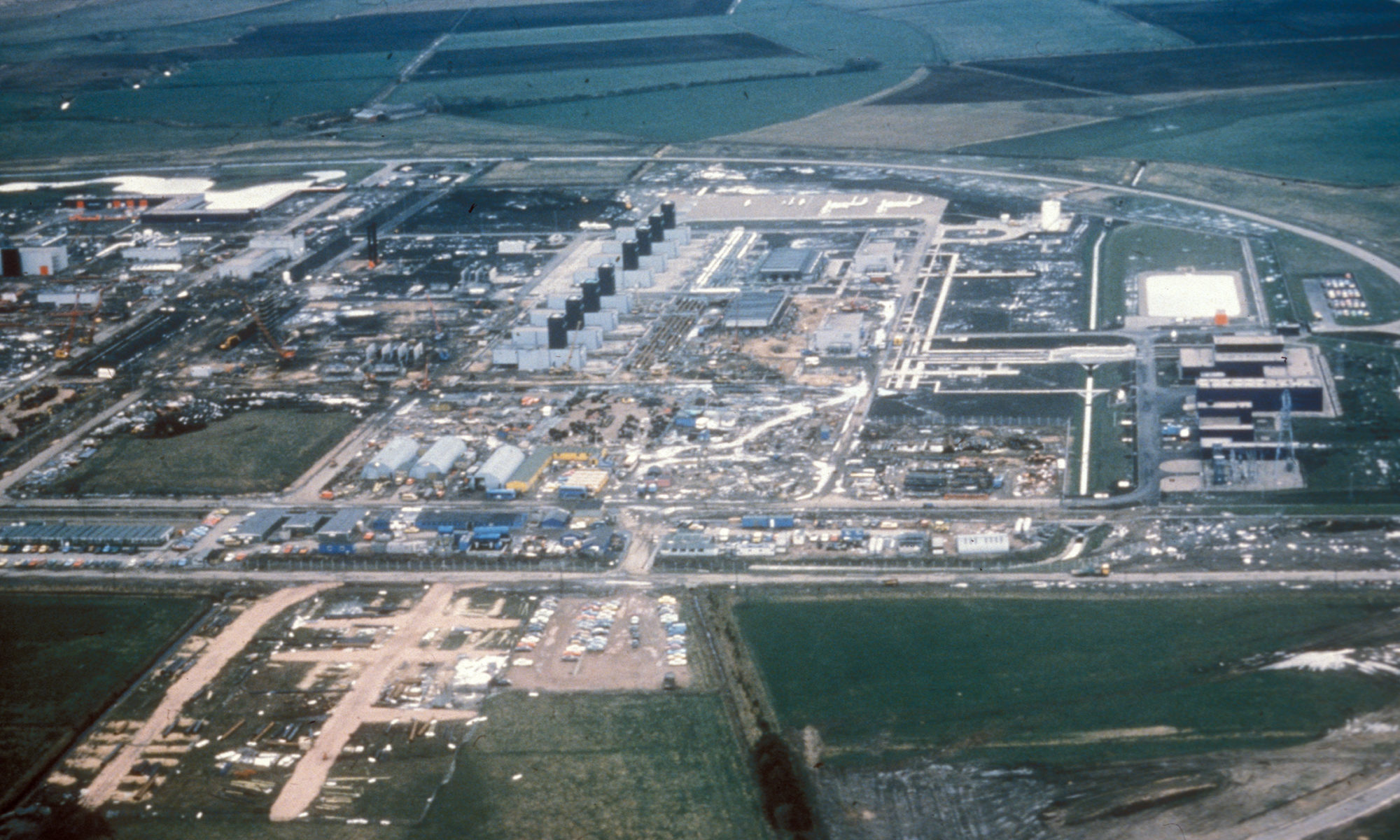
One pipeline was laid for each country. Pipeline 1 is the UK pipeline and is 361 kilometres (228 miles) in length. Pipeline 2, the Norwegian pipeline, is 363 kilometres (229 miles) long. For over 80% of their route, they lie in water with a depth of between 100 and 150 metres (328 and 492 feet), and in places the sea is deeper. This was a world record: pipes this large had never been used at such a depth before.
Previous attempts by other companies to lay slightly larger diameter pipes, had failed. It was decided to build twin pipelines for Frigg – one for each of the partner countries – as a single line would have been unable to transport the anticipated volume of gas, and it was impractical to attempt to lay an even larger pipeline. The pipelines are parallel and 70 metres (230 feet) apart. Any further apart and there would be greater hazard and disruption to fishermen and other companies through whose blocks (areas of the seabed to which the company had exploration/drilling rights) the pipelines passed. Yet they could not be too close, in case work on one pipeline inadvertently damaged the other.
The steel pipes are 2 centimetres (three-quarters of an inch) thick to withstand the internal pressure of the gas. At a plant in Invergordon, Scotland, an anti-corrosion bituminous felt wrap was added. The pipes were further protected from physical damage by a concrete coating reinforced with a wire cage. The heavy concrete also acted as ballast, ensuring that the pipeline did not float up. The seabed along the entire route had been surveyed before construction began, and the thickness of the protective coating on the pipes varied depending on the sea depth and current at the sea bottom. The high current velocity in coastal waters meant that pipes laid for the first 19 kilometres (12 miles) offshore had to have concrete coatings 11.75 centimetres (4 5/8 inches) thick, though in other places only half as much concrete was applied. Perhaps unsurprisingly, each of the 60,000, 12 metre long (40 feet) sections of the pipe weighed nine tonnes (nine tons).
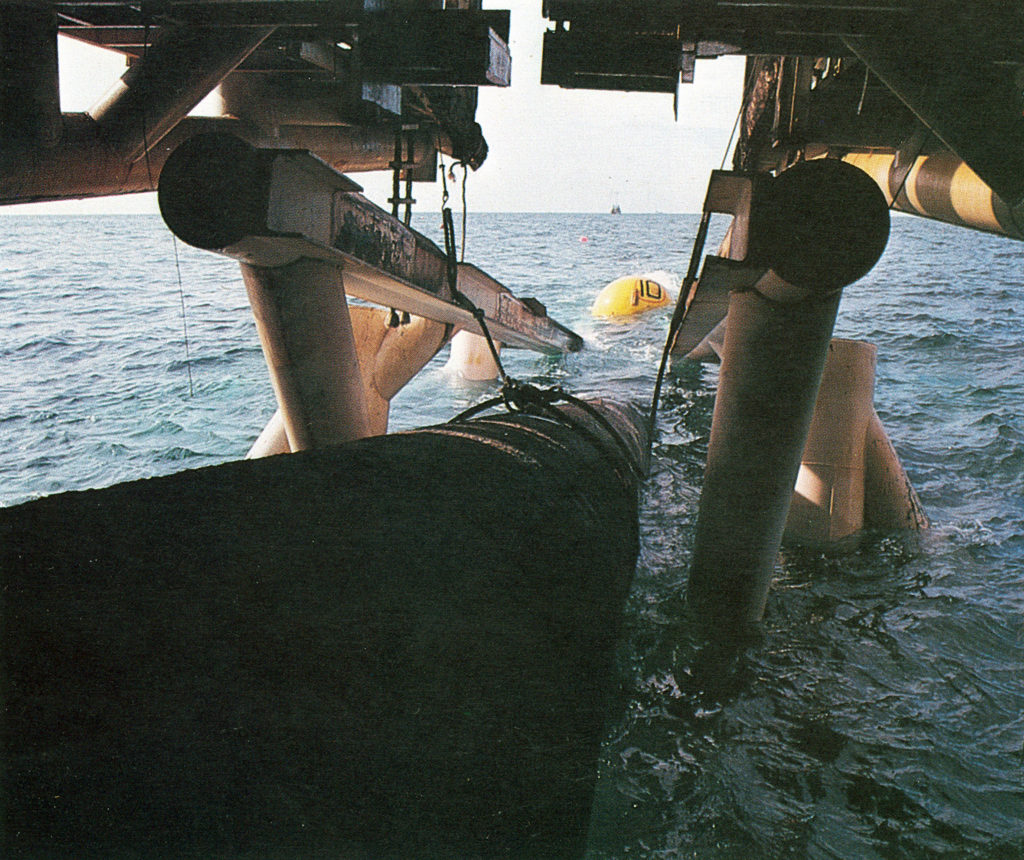
Sections of the pipe were welded together on the deck of the pipe laying barge then fed over the stern from a ramp known as a “stinger”. The barge moved forward as each section was welded on. With one end of the pipe on the seabed and the other on the surface, the pipeline was bent into a slight “S” curve, putting it under stress. The tension was also increased by the motion of the barge due to waves, so pipe laying could only take place when the swell was less than 3 metres (10 feet). Buckle arrestors (sleeves of steel around the outside of the pipe providing extra strength and support) were fitted every fourteenth joint to help prevent the pipe from cracking.
Hyperbaric welding
During previous North Sea operations, the welding had been done manually. Frigg trialled Automatic CRC welding, where machines weld the pipe sections instead of human welders. Automatic CRC welding was carried out by two different types of machine. One executed the root pass from the inside; the other filled the bevel from the outside. It reduced the operating time by 50%, which in turn cut the barge costs. Tests in 1976 showed that all welds were satisfactory in the sections then laid.
It took three years to finish the pipeline, partly because of the distance and partly because of the North Sea’s notoriously bad weather. Even during the summer weather window (April to October) it is still expected that the weather will be too bad for work 50% of the time. Disconnected sections of pipeline were left in position on the seabed to await the return of good weather. Hyperbaric welding was used to join the pipelines laid at different times by different contractors. Hyperbaric welding is welding at high pressure, in this instance, underwater.
It would have been impractical to choose the more usual method of raising the ends and welding them at the surface. Instead, a chamber was installed round pipes to be welded, then brought to ambient pressure by means of a mixture of helium and oxygen – the Frigg pipelaying chamber was the first to obtain a pressure of 15 bar. Divers could then work in a dry atmosphere in relative freedom. Three-man teams did the welding work on the seabed, spending 21 days at a time living under pressure to avoid the stresses and risks of repeated pressurisation and decompression.

Pipeline laying work continued 24 hours a day when the weather was good. The finished work was checked using x-rays, which was the quickest method available, if not the highest quality. It was here that the second world record was broken; that of successfully laying 4.3 kilometres (2.6 miles) of pipeline in 24 hours, which remained until Alwyn North was developed in the late 1980s. Laying three kilometres in that timeframe was considered to be the upper limit of what was achievable.
The pipelines were buried under the seabed to a depth of between one and three metres (up to ten feet). This is normally done by “jetting”: a water jet scours a ditch and an air jet lifts away the excavated sediments, creating a trench in which the pipe is laid. The currents then cover the trench naturally over the course of several days. This protects the pipes from damage, for example by trawlers, and reduces stress caused by freespans. Freespans are when the seabed under a section of pipe erodes, creating a gap where the pipe is exposed and unsupported, which usually has to be filled in with gravel.
The Scottish coast is relatively rocky and subject to strong currents, a combination that made bringing the pipes ashore more difficult. All the coastal pipe-laying was done in the summer of 1975. The closest the pipe laying barge could get to the shore was 1.5 kilometres (0.9 miles). A winch onshore pulled the pipeline in as each section was welded on the barge. Onshore, the pipes are buried to a depth of 2 metres (6.5 feet). This necessitated the removal of the sand dunes but, once work was complete, Total and a group from the University of Aberdeen restored the dunes and replanted vegetation to minimise ecological damage.
Inspection
Maintaining the pipelines is a costly business – in 1980 alone, maintenance cost £4 million. Originally, external inspections were carried out annually as a precaution. After several years this was changed to every two years. Currently, the pipeline is visually inspected by ROV (Remotely Operated Vehicles) and internally on a more periodic basis using intelligent pigs, with the most recent internal inspections taking place in 1995 and 2002.
Several methods were used:
- Acoustic inspections used a sonar scanner towed about 10 to 15 metres (30 to 50 feet) above the seabed to inspect the condition of the seabed, the trench and the pipes.
- Visual inspections usually focus on areas where other inspections, usually acoustic, have identified areas requiring closer investigation. Manned submersibles were used in 1977 and 1978, but following successful trials of unmanned submersibles, these were favoured. Remote-operated submersibles have two main advantages: they can be used for longer periods without risks, and they are more economical – approximately a third less costly per day.
- Electromagnetic surveys are a relatively recent method for surveying the pipeline landfall. These detect the changes in the electromagnetic field along the metal pipe to identify dents, and by identifying the difference between the readings from the pipe and those of the rocks, can calculate how deeply the pipes are buried.
- Onshore inspections are usually either acoustic or electromagnetic and monitor coastal erosion and the movement of the sand dunes as well as the condition of the buried pipes.
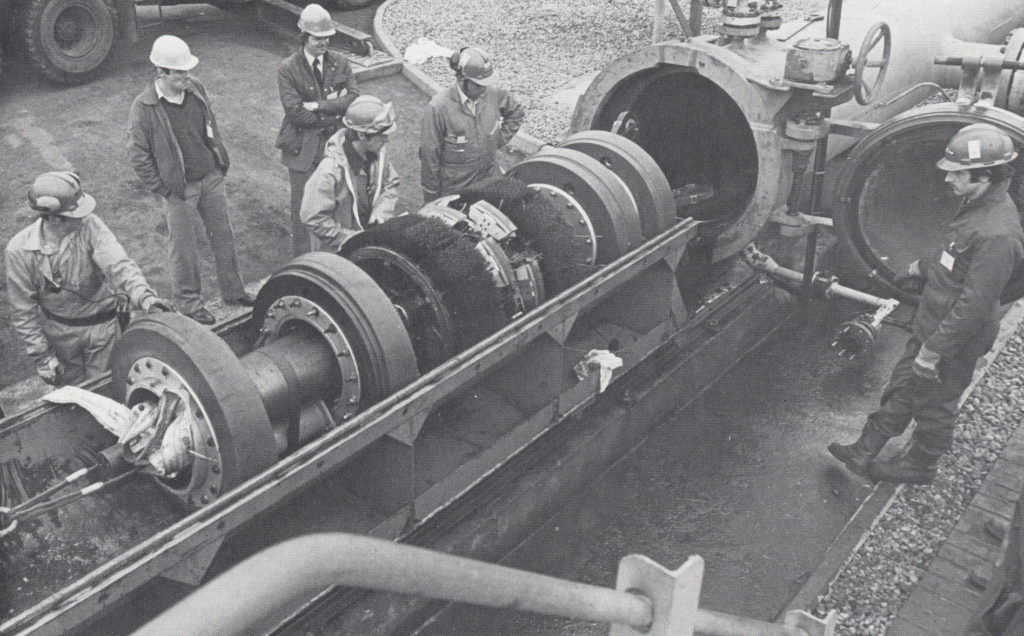
Internally, the FTS is cleaned and inspected using pigs. Pigs are neoprene tools that remove liquid that accumulates in the pipelines and they are also used to check for any internal damage or corrosion to the pipeline. They are built to fit exactly the diameter of the pipes, but otherwise differ depending on their function. Cleaning pigs will have thick, abrasive brushes whereas inspection pigs contain sensitive electronic equipment to accurately record the condition of the pipeline. In 1981, the first intelligent pig went through the pipeline, taking 27 hours to travel from MCP-01 to St Fergus. It was greeted at the terminal by representatives from the Department of Energy and Norwegian Petroleum Directorate.
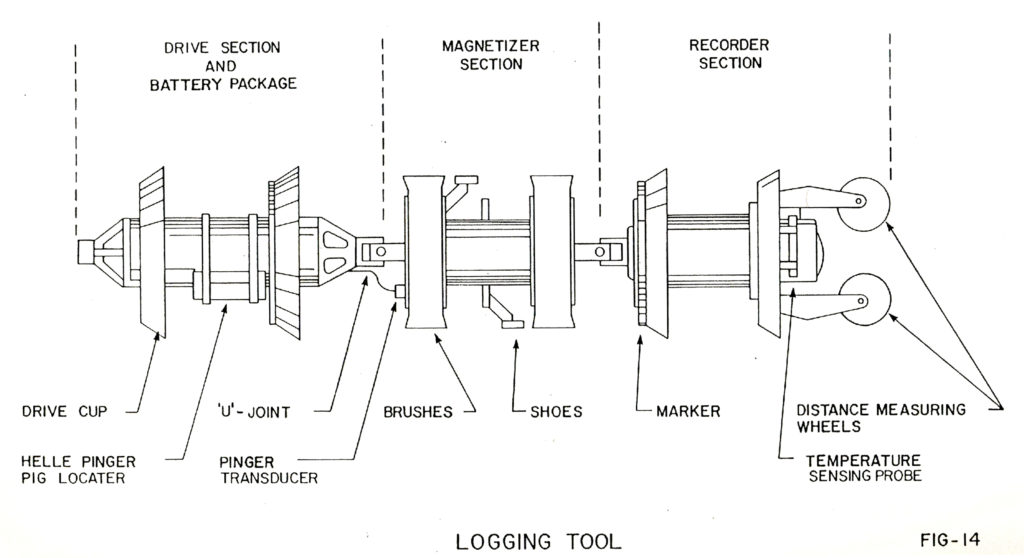
At the time of construction, it was not possible to pig a pipeline as long as the FTS without the pigs becoming worn, and therefore giving inaccurate readings. This was one of the reasons why MCP-01 was built at the mid-point. Worn pigs from Frigg were removed and either refurbished or fresh ones put in to continue down the line to St Fergus.
The whole process used to take two days. Pigs can travel at 5 metres/second (16 feet/second), but for more accurate readings usually travel at only half that speed.
Working Life
On 11 September 1977, the entire Frigg Transportation System and St Fergus terminal was successfully tested to ensure everything was in full working order. Two days later the system became fully operational. Built with expectations of a twenty-year lifetime, it has recently passed its 30th anniversary of continuous service.
The FTS had to be able to cope with the increase in demand during peak times. The pipelines are always kept slightly over-pressurised so that if a compressor or a platform shuts down, there is enough gas already in the system to compensate for a short time without loss of service. This is balanced against a need to prevent the pipes being dangerously over-pressurised.
The UK pipeline has always been owned by Total and its predecessor companies, but the ownership of the Norwegian pipeline has been reorganized. The original Frigg Treaty was updated in 1998.
The decline in the volume of gas produced from the Frigg Field from the late 1980s resulted in the FTS having spare capacity. In October 2001, Pipeline 2 was brought back up to near full capacity with gas from the Heimdal Riser gas platform, in the Norwegian sector. This almost doubled the amount of gas being brought to St Fergus by the FTS. The renaming of Pipeline 2 to Vesterled (roughly meaning “heading West” in Norwegian) followed the connection of Heimdal to the FTS.
Bypass at MCP-01
In order for MCP-01 to be decommissioned, it was necessary for the pipelines, which remained operational, to be rerouted to bypass the platform. The two bypasses are roughly one-mile (two kilometres) long. Pigs marked the places where the pipes were to be cut and the bypass pipe welded on, using hyperbaric welding. Each pig had a tracking device that emitted a unique signal, enabling its exact position to be identified. This was a major operation, as obviously no gas could flow through the pipes whilst the work was underway. The first part of the bypass work was on Pipeline 1 to isolate MCP-01. Subsea 7 was awarded the contract and in March 2004 bundles of pipelines were lowered onto the seabed near MCP-01, ready to be connected to the FTS at a later date. On 26 July, Alwyn, Nuggets, Bruce, Dunbar, Captain and Ross all began shutdown preparations. Production shutdown is a rare occurrence, so much was made of the opportunity to carry out maintenance and repairs on the other platforms, and at the Phase 3 facilities at St Fergus where the gas was received.
Vesterled underwent bypass work the following year, by the same team from Total who had worked on the previous bypass. The pipeline was depressurised on 30 May 2005 and was back at full capacity by 4 July.